With the continuous advancement of technology, CNC machining is proving beneficial across various industries, and artificial intelligence (AI) is playing an increasingly significant role in many fields, including CNC (Computer Numerical Control) machining. The introduction of AI not only enhances production efficiency and precision but also fundamentally transforms the way the manufacturing industry operates. This article will explore the potential applications of artificial intelligence in CNC machining, analyzing its impact on the industry and future development directions.
Intelligent Process Planning
Process planning is an important part of CNC machining. Traditional methods mostly depend on experience and human judgment. This leads to varying degrees of inefficiencies, suboptimal production outcomes, and errors. However, utilizing the Artificial Intelligence algorithms in process planning solves this problem. Engineers can leverage machine learning and data analysis tools to automatically create optimal machining processes.
Data-Driven Insights and Decision Making
AI models can process and analyze significant amounts of historical machining data. They can recognize patterns and gather insights that may not be obvious to human operators. Artificial Intelligence helps in evaluating factors such as machining paths, cutting parameters, and tool selections. Based on evaluation, AI can suggest the most effective strategies customized for specific projects. This data-driven approach is helpful for improving efficiency and also significantly enhances product quality. It is a great tool to minimize variations or defects that might occur in the machining process.
Adaptive Process Adjustment
One of the most significant advantages of incorporating AI into CNC machining is the ability to monitor processes in real-time. AI can regularly track the present machining status, identify any deviations or anomalies if any. This enables automatic adjustments to process parameters like cooling methods, spindle speeds, and feed rates. These automatic adjustments further ensure that that machining remains efficient and stable. Manufacturers can reduce the probability of errors, waste, and downtime and can enhance adaptability. Use of AI lays the foundation for high-quality output.
Predictive Maintenance
In CNC machining, equipment reliability is crucial. Equipment failure not only leads to downtime but also incurs significant economic losses. AI addresses these issues and reduces the likelihood of equipment failure through predictive maintenance. This helps in improving the efficiency of overall production.
Fault Prediction
Fault prediction is at the core of predictive maintenance. AI utilizes the machine learning models, and data gathered from sensors to assess the current operational state and historical performance of the equipment. AI models mainly focus on identifying various anomalies and patterns. This helps in accurately predicting potential failure of an equipment. For instance, real-time monitoring of critical indicators such as temperature, vibration, and pressure can promptly detect abnormal operating conditions.
The effective AI-based warning system gives technicians time to replace certain components, repair parts, or fix other issues that might lead to failure. Manufacturers can thus reduce the possibilities of downtime and prevent losses. Moreover, accurately predicting fault and failure improves its lifecycle of the equipment and ensures its availability. Manufacturers can also save on maintenance costs over time as the need for emergency repairs reduces. They need to just invest on planned maintenance, which is generally more economical.
Optimizing Maintenance
One of the crucial aspects of long-term efficient operations is maintenance optimization. AI algorithms can easily analyze maintenance history, environmental conditions, and operational information. Thus based on insights and thorough analysis, they can provide smart maintenance schedules. Through AI, manufacturers can find out the right time for maintenance and reduce chances of production disruptions.
This intelligent maintenance upgrades the way manufacturers handle equipment and significantly improves its shelf-life. For example, based on specific usage patterns and load conditions, AI can recommend optimal maintenance cycles and strategies, ensuring that equipment operates in peak condition. This in turn gives companies insights to better allocate resources and streamline the use of labor and materials. This empowers organizations to thereby boost overall efficiency of production and get good economic returns.
In summary, predictive maintenance utilizes the capability of artificial intelligence to make CNC machining equipment much more dependable. This ensures that companies donβt encounter unexpected equipment failure and get greater economic value over time.
Quality Control
Product quality is an important parameter of manufacturing, which directly impacts end-user satisfaction and brand reputation. In the competitive landscape of CNC machining, ensuring consistent quality is paramount. Artificial intelligence (AI) enhances quality management throughout the CNC machining process through intelligent quality control systems.
Online Inspection
AI can seamlessly integrate with machine vision technology to enable online inspection and monitoring. Artificial Intelligence can easily integrate with high-resolution cameras and image processing tools to examine product images in real-time. This feature of AI helps in immediate identification of variations like dimensional errors, imperfections in surface, or inconsistencies in material.
For instance, if a defect is detected during the machining process, AI can trigger immediate adjustments to the machine settings, such as altering cutting speeds or tool paths, thereby preventing the production of defective parts. AI tools make companies proactive and ensure that no equipment is wasted and only great quality products are approved through the production line.
Data Analysis
Apart from excelling in real-time analysis, AI also conducts in-depth analyses of key data to recognize important factors affecting quality of the product. AI tools can easily accumulate data from a number of sources like operator logs, machine sensors, and historical records. AI can then find out patterns and correlations that might be missed during manual analysis.
This feature of AI assists manufacturers in further streamlining machining processes depending on targeted insights. For example, if analysis reveals that certain cutting parameters consistently lead to defects, adjustments can be made to improve those parameters across the production process. AI is also capable of finding out the main reasons for quality issues through root cause analysis. Using this, manufacturers can understand the main areas they need to work on and can then take necessary steps.
Continuous Improvement
AI-driven quality control fosters a culture of continuous improvement within manufacturing operations. AI helps in creating a feedback loop where relevant data from inspections informs are utilized in future production planning. In this way, manufacturers can improve their processes and techniques over time. As a result, companies can maximize their operational efficiency and production quality. Economic benefits of this are improved profit margins and reduced costs of production.
In summary, the significance of AI lies in upgrading the quality control in CNC machining. AI integrates online inspection capabilities and holistic data analysis to give the desired results. From recognizing key defects in real-time to providing valuable insights, AI is relevant everywhere. AI can help manufacturers maintain high quality standards, reduce wastage of materials, and establish an environment of regular improvement. Ultimately, AI plays a crucial role in ensuring superior product quality, higher customer satisfaction, and a better credibility in the market.
Production Scheduling Optimization
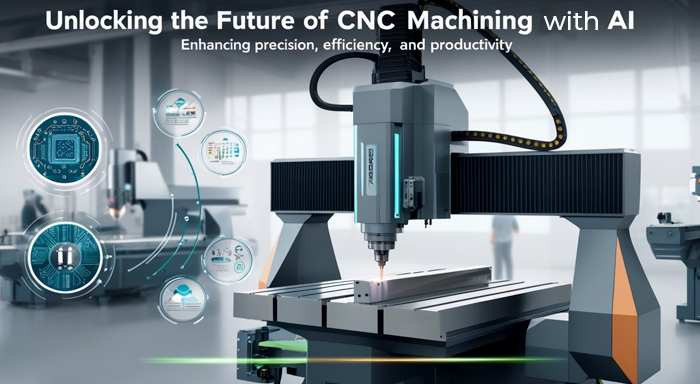
CNC machining often involves multiple processes, machines, and resources, making production scheduling a complex and challenging task. Efficient scheduling plays a crucial role in increasing productivity and reducing expenses. Artificial intelligence (AI) is capable of upgrading production scheduling through effective algorithms. This leads to higher overall efficiency and adaptability to changing conditions.
Intelligent Scheduling Systems
AI-driven intelligent scheduling systems can automatically generate optimal production schedules by considering various factors such as order priorities, equipment statuses, worker availability, and even material supply chains. These systems leverage advanced algorithms that examine present conditions and historical insights to create schedules. This helps in minimizing bottlenecks and that minimizes bottlenecks and cuts down idleness.
For example, when a new order is received, the system evaluates the urgency of the order, the availability of machines, and the skill sets of workers to create a prioritized schedule. This ensures that manufacturers are processing high-priority orders first. Manufacturers can then make the use of resources more efficient. This allows organizations to minimize wait times and improve production efficiency. Additionally, the AI systems are also capable of providing insights into probable delays. This helps managers to quickly analyze the situation and make informed decisions.
Dynamic Adjustments
One of the most significant advantages of AI in production scheduling is its ability to make dynamic adjustments in real time. During production, AI models regularly track progress, performance of the equipment, and any problems that can arise like machine breakdowns or unexpected delays. When a deviation from the original schedule is detected, the system can automatically adjust the scheduling plans based on actual conditions.
For instance, if a machine encounters a malfunction, the AI can reroute tasks to alternative machines or adjust the order of operations to maintain workflow continuity. This flexibility helps managers manage downtime and respond to changes in demand or production capabilities quickly. AI gives companies capability to adapt to schedules in real-time, ensure high levels of efficiency and continuously meet delivery deadlines.
Enhanced Forecasting and Planning
Moreover, AI can enhance production planning through predictive analytics. AI utilizes historical data and trends to accurately predict future demand and patterns. This enables manufacturers to foresee fluctuations in workload and prepare well in advance. This foresight helps organizations become more proactive in managing resource allocation and workforce. This empowers organizations to optimize their production process even further.
In short, AI plays a crucial role in optimizing production scheduling in CNC machining through intelligent scheduling systems and allowing quick adjustments during production. By streamlining the scheduling process depending on real-time data and order priorities, manufacturers can maintain total flexibility, improve efficiency, minimize wait times in the event of changing conditions. This puts organizations in a good position to utilize resources efficiency, streamline operations, improve satisfaction of the customers, and compete well in the market.
Personalized Manufacturing
As customer demands continue to diversify, personalized manufacturing has emerged as a prominent trend in the industry. Nowadays, companies need products that have specific features and meet all their preferences. This has given rise to customized manufacturing. Artificial intelligence plays an important role in enabling personalized manufacturing. It allows manufacturers to meet specific demands of the customers more effectively. It not only makes the manufacturing process more streamlined and organized, but also reduces costs of production.
Customer Demand Analysis
AI models contain features that analyze customer data and recognize potential preferences and needs. You can utilize quality data from various sources like purchase history, market trends, and customer feedback. It then utilizes advanced data analytics techniques to process vast amounts of information. This is a powerful way of gaining valuable insights into evolving customer preferences and demands. Manufacturers can foresee demand before they arise.
For example, recognizing trends in customer preferences for different product features, organizations can design personalized production plans that meet customer expectations.This makes organizations more proactive and attentive to customer needs. AI can also suggest ways to companies to personalize their services to satisfy different customer segments. It is a powerful way of making customers feel that the organizations cares about them, ensuring brand loyalty.
Custom Design
AI is also a relevant tool for designers in designing custom products. AI offers automatically generated design options as per specified criteria. Then utilizing machine learning algorithms, AI can examine existing designs and customer insights to provide a range of customized design options. This feature helps in reducing the number of design cycles. It further makes manufacturers capable of responding to customer requests for customization more quickly.
For instance, if a customer requests a unique feature for a product, the AI system can generate multiple design options that incorporate this feature while considering manufacturing constraints. AI makes the design process more organized and automated. This empowers designers to pay more attention on core tasks rather than getting involved down in repetitive tasks.
AI contains interactive design elements that ensure easy collaboration between designers and customers. AI allows customers to give feedback on AI-generated designs in real time. Thus, it helps in making the design process more responsive and dynamic. This collaboration is essential not only in making personalized products but also in raising customer engagement and satisfaction.
Efficient Production and Supply Chain Management
To fully realize the benefits of personalized manufacturing, AI can optimize production processes and supply chain management. Manufacturers need to integrate customer demand analysis with production scheduling to make their operations aligned with personalized orders. AI tools are competent to predict required resources, equipment, and materials.This enables lower lead times and organized inventory management.
This integration is quite vital in ensuring that manufacturers can produce personalized products without compromising on efficiency. For instance, when a personalized order is received, AI can adjust production schedules and allocate resources accordingly, minimizing disruptions and maximizing output.
In summary, AI is a right tool to have for customized production, improving analysis of customer demand, custom design processes, and overall efficiency during production. Through utilizing data-driven insights and automating generation of design, manufacturing teams can better satisfy the diverse expectations of their customers. This change toward personalization improves the overall satisfaction-level of the customers. This also empowers organizations to position themselves more competitively in the market. Integrating AI in customized manufacturing is quite key to reach goals in the future landscape of the industry.
Future Outlook
As artificial intelligence technology continues to advance, its future trends in CNC machining are also evolving. In the future, AI may enhance its value in the following areas:
Integrated Systems: The combination of AI with the Internet of Things (IoT) and big data can lead to more intelligent production systems that collect, analyze, and feedback data in real-time, forming a closed-loop control system.
Smart Collaboration: Combining AI with robotics is quite effective in allowing automated processes in CNC machining. Smart collaboration helps in improving overall flexibility and production efficiency.
Human-Machine Collaboration: AI will further advance human-machine collaboration, allowing human workers to focus on more creative and strategic tasks while delegating repetitive tasks to machines.
Conclusion
In todayβs manufacturing industry, no tool is more powerful than AI. It is a game-changer when it comes to personalized manufacturing, improving customer preference analysis, custom design processes, and upgrading overall production efficiency. As a manufacturer, you can utilize data-driven insights and automate various processes to satisfy your customers. Customized marketing has become greatly important in todayβs market due to evolving customer demands. You need AI not only for customized manufacturing, but also improved customer satisfaction, and establishing competitiveness in the individualized market. AI is a relevant technology for businesses to grow in the manufacturing industry in future.Β